There are many surface treatments and finishes common to the mixing industry. The most common and popular include:
- Surface Treatments
- Polishing
- Coatings
Surface Treatments
Surface treatments are performed on metals to achieve a certain quality that makes them compatible with the process to which they they are exposed. There are numerous treatments available for materials. In the mixing industry, the most common treatments are passivation and electropolishing. Passivation and electropolishing are commonly performed on pharmaceutical mixers, shafts, and impellers.
Passivation
Passivation is a process that removes excess or “free” iron from the surface of stainless steel. In the case of mixers, many components are welded, machined, sand blasted, and/or mechanically polished. Passivation removes the free iron that is left on the surface by these operations.
The Passivation process begins by cleaning the stainless component. After the part is thoroughly cleaned, it is immersed in a hot bath of nitric or citric acid for a period of a couple hours. What results is an ultra-thin layer of chrome oxidation on the metal that acts as a protective coating. Nitric acid passivation typically yields better results.
Polishing
Polishing the surfaces of a mixer's wetted parts is done to promote clean-ability and to reduce contamination from unwanted components or bacterial growth. Although most commonly done for the food and pharmaceutical industries, polishing is also utilized on applications that require thorough cleaning to reduce contamination. Polishing of mixer parts is typically done by first performing a mechanical polish, and then, in some cases, followed up by passivation or electropolishing.
Mechanical Polishing
Mechanical polishing is done by grinding irregular surfaces of the mixer wetted parts to achieve a smooth finish for clean-ability and sanitary operation. Coarse stones, grinding wheels, and grinding belts are used to grind off welds and to remove porosity. Successively finer abrasives are used until the desired result is achieved. In the case of super fine finishes, flannel wheels are used with rouge compound to “buff” the part. Some customers do not allow the use of rouge type compounds, as they sometimes contain animal fats.
ElectroPolishing
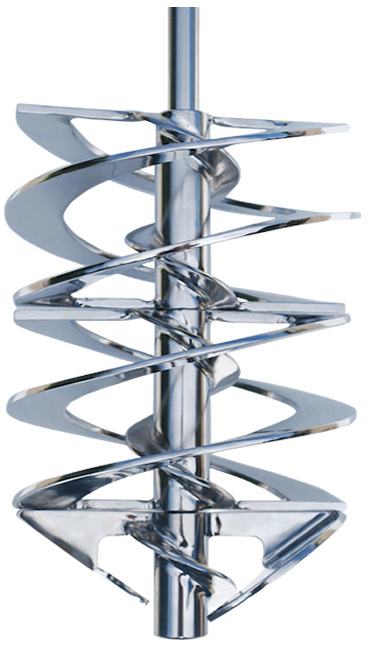
Electropolishing is done by soaking a part in an electrolytic chemical bath with anodes. Electropolishing serves two purposes. The first accomplishes the same as passivation. A chrome oxide skin is formed on the surface of the metal that acts as a corrosion-resistant layer. Free iron is also removed (just like passivation). The second benefit is that it polishes the surface of the metal. The electrical current knocks the “high spots” off of the metal and improves the quality of the finish. In some cases electropolishing can take a part that is initially finished to 15Ra micro-inches and improve the surface quality to 8Ra micro-inches.
Coatings
Depending on the application, sometimes an additional coating is applied to the surface of the mixer’s wetted parts. Coatings are typically applied for corrosion resistance, abrasion resistance, or for easy cleaning. There are many options to choose from depending on process requirements and budget.
Rubber Coating
Used in applications requiring abrasion resistance, Natural Rubber has great elastic properties and bonds well to metals; however the coating does not fare well with oxidizing chemicals, oxygen, ozone, oils, or solvents.
ChloroButyl Rubber has similar properties to natural rubber with much more tolerance to chemicals, solvents, and oils. Applied in sheets and vulcanized, ChloroButyl (or butyl) rubber offers a thick and durable coating to mixer wetted parts. This is a good coating for applications where mixer parts are regularly moved around and used vigorously.
PVC Coating
A low cost coating for mixer parts to be “dipped” into. This plastic coating forms a protective shell around the wetted parts. PVC has excellent chemical compatibility with many chemicals including several acids. Often overlooked, it is a good durable coating that should be considered first before spending money on Teflon-based coatings.
Cold Tar Epoxy Coating
One of the lowest cost coatings commercially available. This epoxy coating can be painted on mixer parts with a brush and cures within hours. It is a great, low cost option to protect wetted components in lightly corrosive environments. Commonly used on large turbine agitators in waste water treatment applications, cold tar epoxy is applied in the field to carbon steel turbine blades, the mixer shaft(s), and other hardware. It prevents excessive rust and lengthens the lifespan of the mixer. As this coating is not extremely durable, it is not recommended for highly corrosive environments, or applications that require any amount of abrasion resistance.
Kynar Coating
Kynar is a high purity fluoropolymer coating that is suitable for many pharmaceutical, nuclear, and chemical applications. Also known as PVDF, Kynar offers superior chemical resistance and durability at a lower cost than other high end coatings. In addition to the ability to be used as a coating, Kynar can also be molded and machined. This makes Kynar a great candidate for composite mixer materials of construction. Solid Kynar impellers can be used in conjunction with coated or sleeved mixer shafts.
Halar Coating
Haylar (ECTEFE) is another coating with great chemical compatibility. It forms a very smooth surface with reduced risk of pinholes, making it easy to clean and resistant to build up from process material. A great option for Hydrofluoric Acid, Sulfuric Acid, Nitric Acid, Hydrogen Peroxide, and Alkaline chemistries.
PFA Teflon Coating
PFA is the lowest cost Teflon based coatings for mixer parts. Typically applied in powder form and baked on to the shaft and impeller, PFA offers superior chemical resistance at a reasonable price. The downfall is that the coating is typically only 5 mils thick, so parts have to be handled with care and never used in abrasive mixing applications.
ETFE Teflon Coating
This thick, opaque bluish-white Teflon-based coating is a high purity, rugged coating with superior chemical resistance. It is a favorite for the pharmaceutical industries, as it can be provided with USPVI as well as BPE pharmaceutical conformance documentation. As cost is higher than most other coatings, it is recommended for long term service where durability and clean-ability are paramount.